来源:https://zhuanlan.zhihu.com/p/692917694
由于技术水平有限,发布于此请各位大神指教一二。
1 整机介绍
本次拆机的机型为思灵Diana7(21年7月生产)的2轴关节,整机参数如下
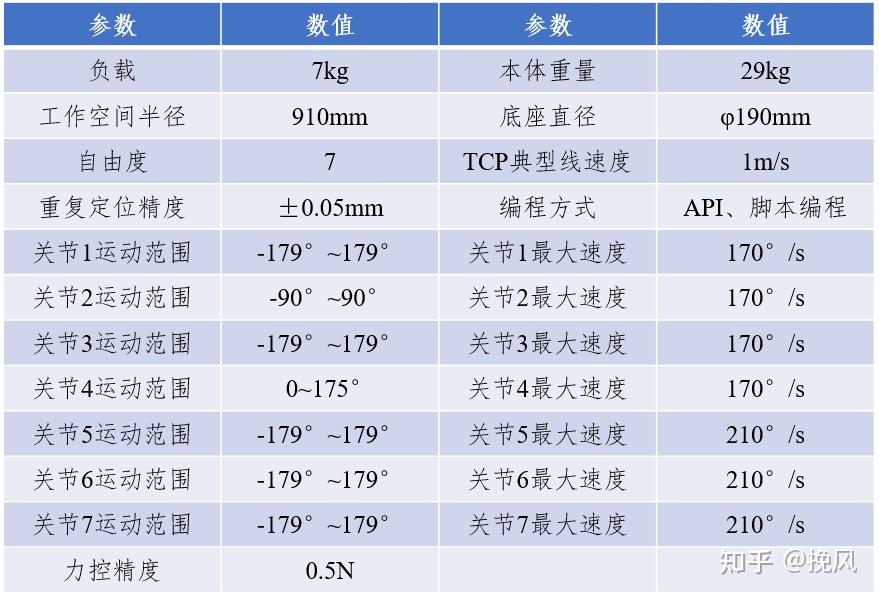
该机型为7自由度协作机械臂,整机构型为iiwa基本构型,属于七自由度逆解空间的早期经典构型(逆运动学解析解的充分条件是Pieper准则,即三个相邻关节轴交于一点或者三个相邻关节轴相互平行),其基本特征为各相邻关节互相垂直,是在六自由度的最佳位置构型的条件下J2、J3关节中间加入了一个横滚轴得到,又称为SRS型,冗余的自由度可用于本体避奇异、避障、避限位、增加操作灵活度等任务。
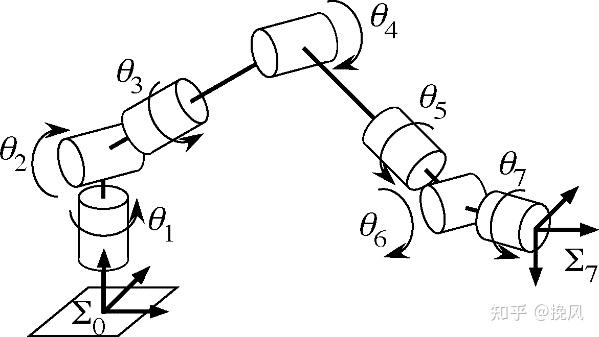
问题:
Q1——关节最大速度是如何设定的,为何J1-J4为同样的速度,J5~J7为同样的速度,其与运动规划是如何制约的?
Q2——运动范围均未超过180°,为何超过180°会丢零点?
2 关节整体结构
拆解的J2关节类似专利[1]所提的图示结构,从左侧 到右侧依次为输出法兰、交叉滚子轴承、谐波减速器、输入轴、电机单元、高低速编码、驱动控制板等结构。

2.1 驱动控制组件
思灵单关节的驱控一体板各电路功能分区如下(了解不多)
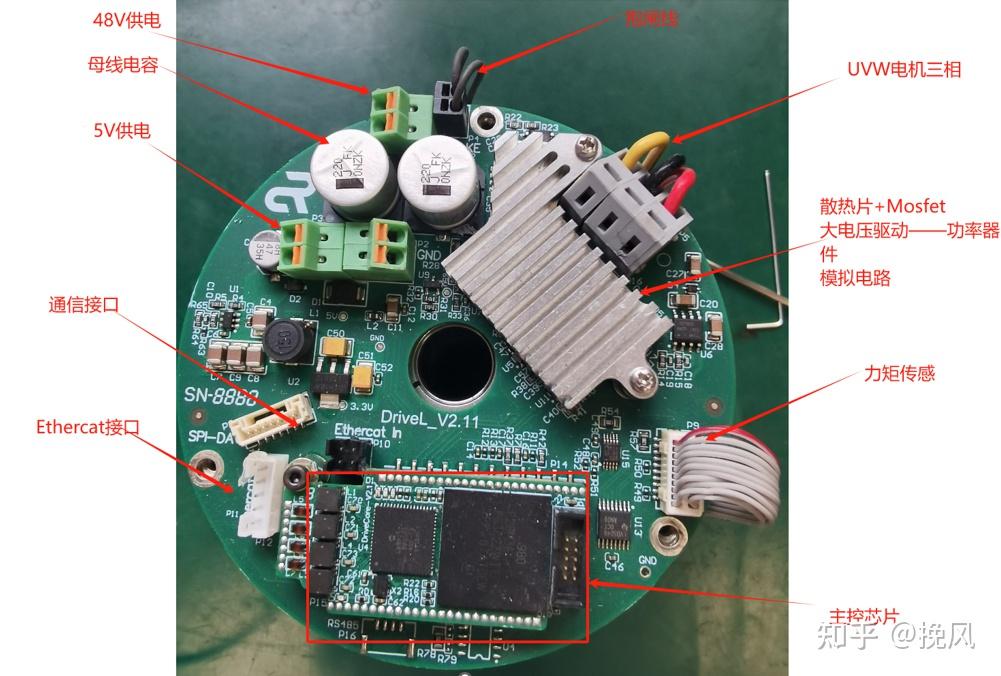
2.2 固线板
固线板主要是用于穿过中空线筒的线束的固定,功能可分解为:
- 固定线束的方式——扎带捆绑,需要防止扎带的滑动,可以通过在捆扎位置增加防滑动凸起、或者固定位置增加孔洞以固定扎带。
- 减少线束因转动的磨损——线束居中性设计:一方面可以通过将中空线束设计为双绞线,在旋转过程中自行调节长度(但是容易与中控线筒筒壁摩擦干涉,且增加线长后对通信及成本会有影响);另一方面可以通过弹性补偿机构来实现,比如轴向弹性补偿(UR关节的挠性板似乎采用的就是弹性补偿)
- 避让驱控板插线:图4所示固线板的形状(左边和上边)弧度为避让驱控板上的母线电容与Ethercat插口;中空空处的豁口是为了装配方便预留(当线束穿过中空橡胶圈时,橡胶圈会被撑大,从而无法直接装配上去,不知道通过合理选型是否能够解决这个问题,因为这个豁口让线束也很容易在旋转中脱离,从而增大摩擦)。
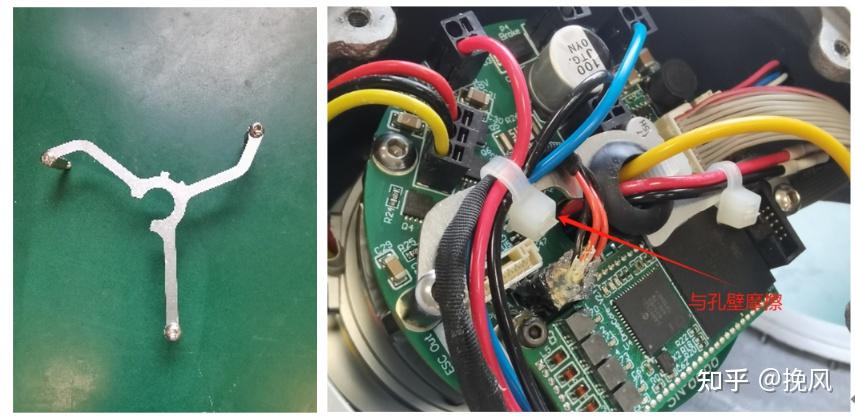
2.3 低速端编码
低速端编码组件分为动件(磁环)和静件(磁编传感),参看图2专利结构图,磁环通过轴承(型号为61803)固定在中空线筒上(外圈与电机外壳固定,内圈与磁环配合,均为松配),其轴向配合关系细节如图5所示,动件磁环通过轴承轴向固定在电机外壳上,静件磁编传感通过电机外壳上的凸台轴向固定,从而只需要保证电机外壳的轴承挡肩位置与凸台位置的加工形位公差,就可以确保磁环与编码器之间的相对轴向间距。
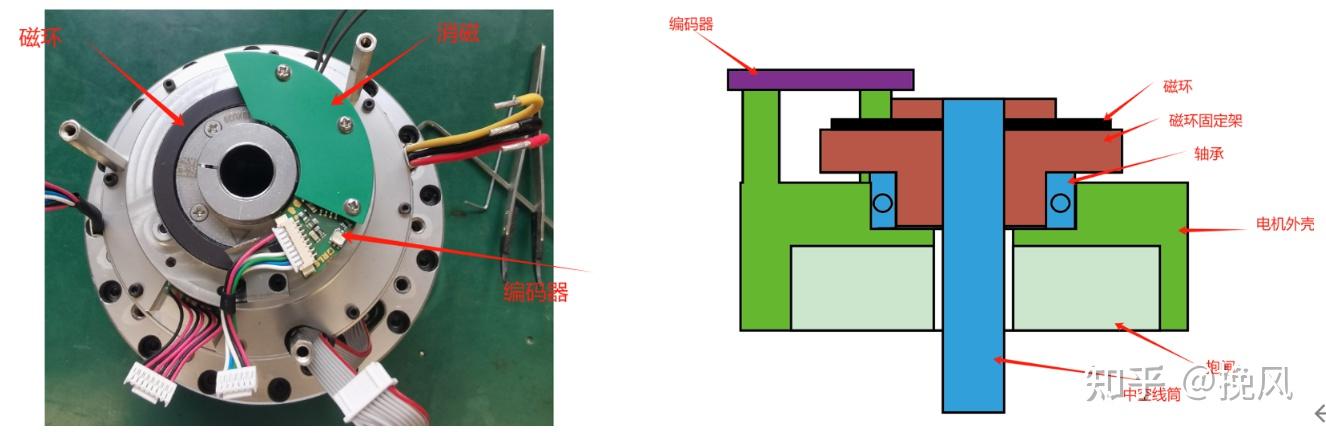
上面有一部分扇形件应该是消磁挡片。任何磁编码器的工作原理都是感应磁环的磁场变化,因此必须阻断不必要的磁场源,如果无法阻断,需要使用铁磁金属板来屏蔽编码器,磁环本身也可用于局部屏蔽,通常将磁环底部朝向泄露磁场源安装,而读数头背向磁场源。另外,该编码器的正上方是MOSFET功率器件,属于模拟电路,可能会存在电磁干扰,故而猜测这一扇形件用于消除磁场干扰。
低速编码传感采用的原理磁环为平面充磁,主要回路为垂直于纸面方向,两个正交90°的线性霍尔芯片放于磁环平面之上(装配时需要保证芯片与磁环之间的相对距离,该间距误差越小,编码器精度越接近出厂标定值),分别得到一个周期的磁场强度波形,这两个正交的波形使用arctan(y1,y2)可以得到360°中的唯一对应值,该编码器为绝对编码(若为单个霍尔芯片,则为增量编码)。但需要注意的是,单对极磁编码器的物理精度有限,比磁游标细分、磁刻线细分方案的绝对定位精度要差得多。通常来说,协作关节在选用输出端(低速端)编码器时,直接测量的是输出位置的变化,其分辨率需要匹配扭矩测量的分辨率(扭矩测量指测量外界微小力的变化),因此追求的是高分辨率而不是绝对定位精度。
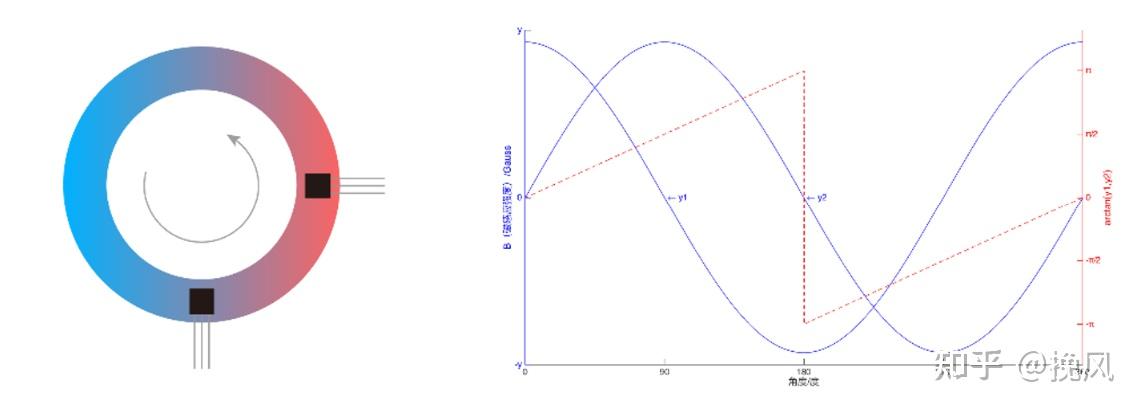
此处编码器磁环的轴向锁紧采用的是紧定抱箍,相比一对垂直方向的紧定螺钉来说同轴度偏差会小一些吧;另外线束固定时为了避免碰到磁环,使用了线束支架以分离线束做避让(线束共有6根线,2根电源,2根输入输出,1根状态线—用于判断是否正常工作,1根MISO数据线—非正常工作的报警数据)。
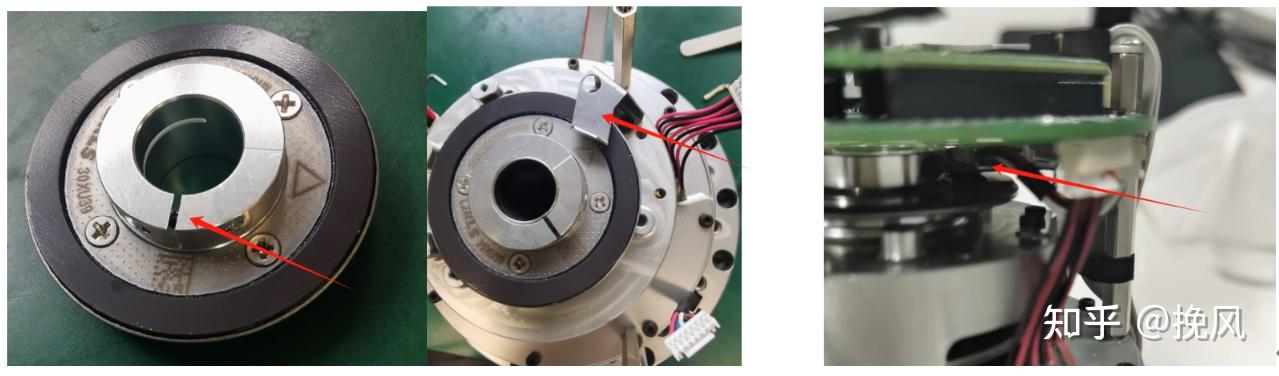
2.4 抱闸
前文所述电机外壳上部固定有电机抱闸,抱闸采用的是电磁摩擦片式,不通电的时候,由于扭矩弹簧的作用,衔铁压住转子,通过所产生的摩擦力对轴伺服电机轴进行制动和保持;当线圈通电时,衔铁在电磁力作用下压缩弹簧,转子被释放,可以自由旋转。
在进行抱闸选型时,一般来说,经验上会提到抱闸力矩约为电机额定力矩的1.3~1.5倍,但是实际上制动力矩并不完全参考电机的额定扭矩,而是令其最大值和最小值满足一定的条件:
最大值:制动力矩必须低于减速器的启停扭矩,否则急停断电的时候制动扭矩过大会造成减速器损坏或者关节偏移,因此其高值不能大于减速器启停扭矩。
最小值:制动时需要具备断电保持姿态的能力,则制动扭矩必须大于负载扭矩(包括末端负载和自重负载),因此其低值不能小于负载转矩。
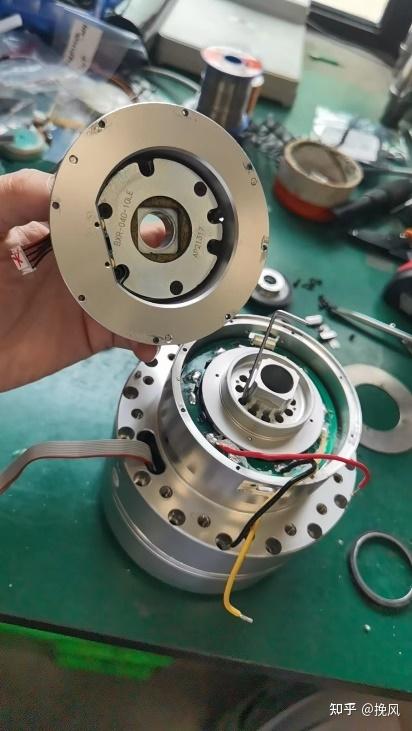
2.5 高速端磁编
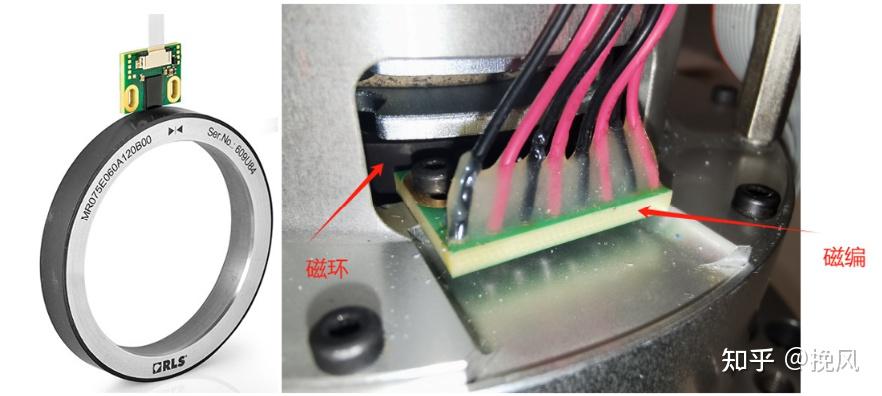
高速端磁环采用轴向充磁的方式,磁主要回路为径向回路,相应的读头放在回转方向的径向位置,为增量式磁编传感器。该关节的磁环采用粘结胶粘在电机转子轴毂上,此外还可通过端面螺钉锁固方式。
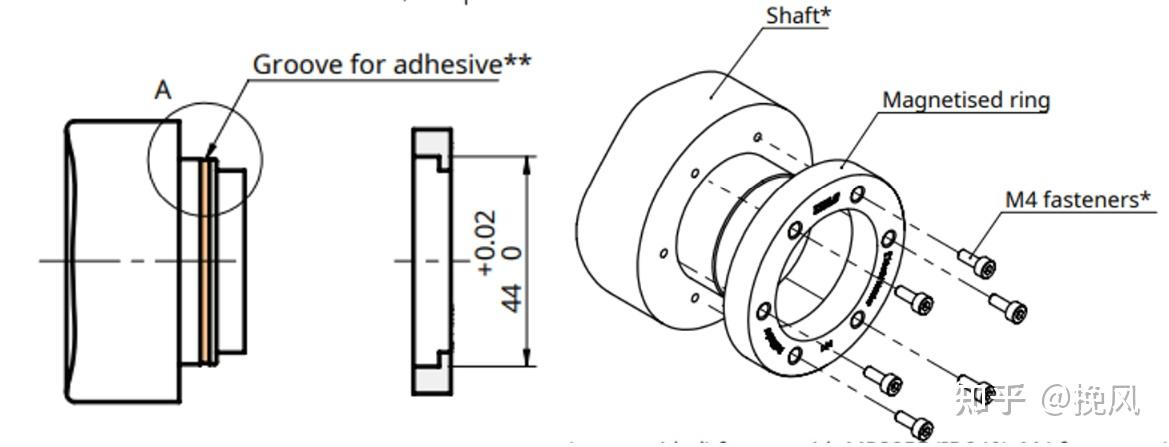
关于安装误差,径向读数的磁编其误差主要是径向中心偏差与轴向高度偏差,如图9所示。其中,U形孔位可用于校正读数头相对磁环的径向位置,但需要确保设计安装时参考磁环手册确认安装轴的配合公差;对于轴向高度的偏差,该关节采用固定抱闸所在外壳的位置上一处加工面来保证
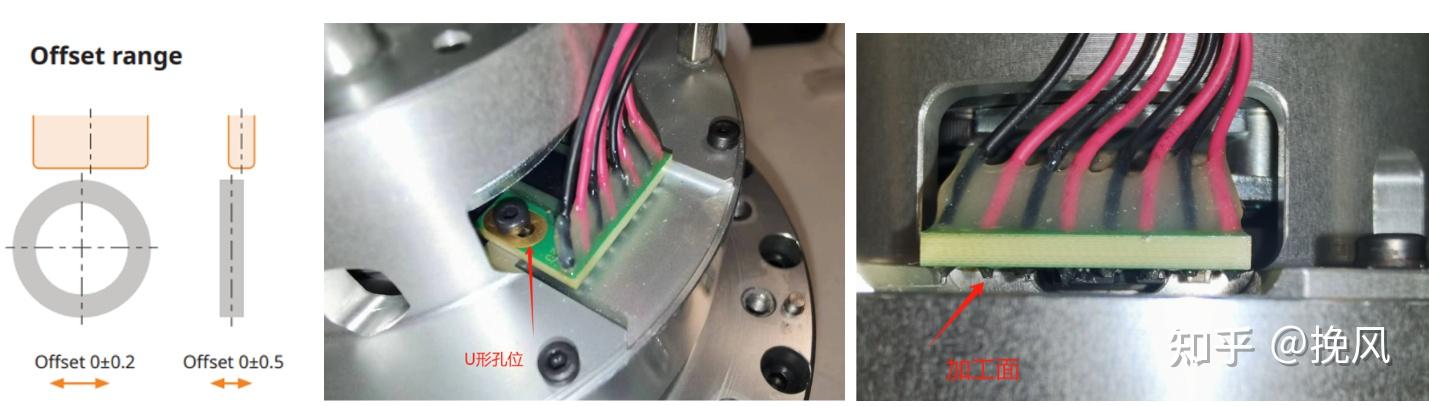
2.6 电机单元
电机组件包括电机外壳、电机轴、输入轴、电机定子、电机转子。电机定子与电机外壳固定连接,电机转子与电机轴固定连接,电机轴与输入轴固定连接(电机的定子和转子我未拆成两部分)。值得注意的是,一方面在电机轴承上加了波形弹簧和精密垫片;另一方面该电机绕组上还带有霍尔传感。其次,还需要注意到,该关节的轴承是在非驱动端(电机与减速器之间),类似于普通电机的轴伸端,电机转动产生的转矩通过轴伸端传递给外界负载,轴伸端的轴承需要承受外界负载和电机转子的重力的径向负载(卧式条件),此外还会受到电机由于温升膨胀引起的轴向尺寸(轴向窜动差异较大),因此轴承总体来看收到轴向和径向的双重载荷。此处关节选用的轴承为61806轴承,内圈为紧配合(很难取下来),外圈为松配。
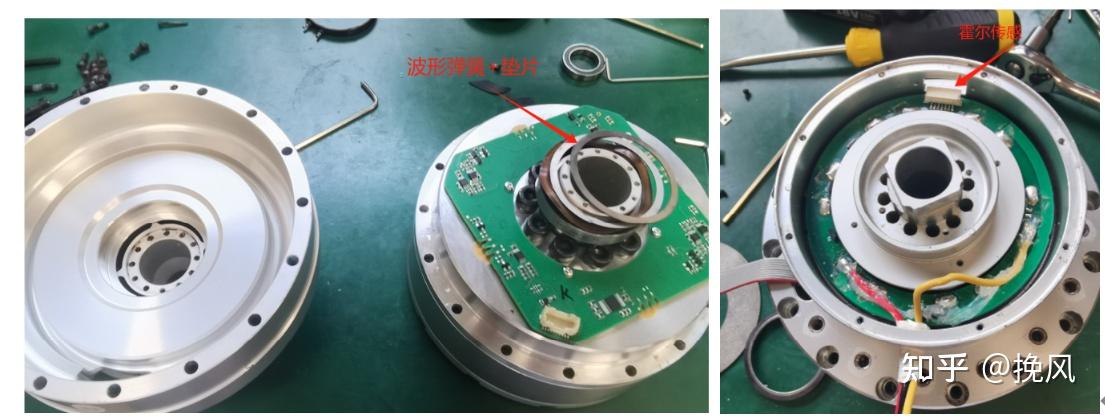
(1)电机轴承波形弹簧
经过调研学习发现,很多电机轴系统中都对电机轴上的轴承(尤其是深沟球轴承)施加预紧力,使用的多数是波形弹簧,对于一些较大的电机则用柱形弹簧。这种预紧可以将轴承的游隙控制在0以下,减少滚动体在滚道之间的运动空间,可以起到降低噪声的作用(很多轴承施加预载荷都是为了减少轴承噪声);其次,施加预载荷可以抵消由于加工及温差引起的轴向窜动或载荷,增加系统的刚性,此外,由于柔轮的弹性形变,运转中谐波减速器的波发生器轴向力朝向柔轮膜片方向,波弹也可以用于抵消该轴向力。
由以上调查到的原因来看,第一个目的减少轴承噪声,对于协作机械臂来说,降噪似乎是必须的,但是这会给轴承造成一定的轴向负荷,应该会影响轴承的寿命;第二,从系统刚性来看,波形弹簧本身属于一个弹性体,在外界运行工况较恶劣时,反而会让电机轴系统成为一个弹性支撑系统。
因此,波弹的存在既必要同时也存在问题,波形弹簧的选用计算就十分关键了。
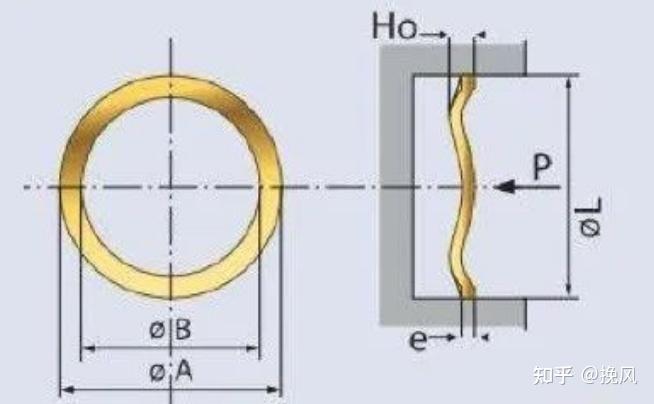
该关节电机所咏波形弹簧外观如图11所示,常用于负荷和变形量不大、要求弹簧刚度较小、存在一定轴向力的场合。由上述分析,波形弹簧的主要作用是为了给电机轴系统一个轴向力,这个轴向力即波形弹簧通过轴向压缩变形产生的弹力。该弹力的大小应当等于所需要施加的预负荷值(但需要保证该弹力在轴承需要的轴向预负荷范围内)。在该预负荷值的条件下,会对应波弹的试验高度(变形后的高度),再依据该高度值计算电机轴承与电机轴系统之间的间隙,然后通过增加精密垫片来补充间隙。
精密垫片的准确添加将影响到波形弹簧的寿命与有效性,波形弹簧在变形范围内不应该出现断裂或者弹性巨大变化,但是如果变形范围过大将会引起波弹失效,从而影响电机轴系统。
(2)电机上的霍尔传感
无框力矩电机由驱控板供电控制U、V、W三相电形成电磁场,永磁铁的转子在此磁场作用下转动,霍尔元件或另外加装的磁编用于反馈信号,驱动器根据反馈值与目标值进行比较,调整转子转动的角度,达到伺服控制的目的。
电机板上带的霍尔属于开关霍尔,只能检测转动一圈中的几个位置,使用该传感器只能通过方波驱动(六步换向);而加装的磁编是用于感知一圈中的任意角度,可以通过正弦波驱动(FOC控制),因此该霍尔元件的作用有两个:一个是为了在电机端编码器标定时使用霍尔先让电机转动起来,另一个是为了编码器失效时使用霍尔冗余备份。
(不知道该霍尔元件是否可以起到消除抖动的作用)
2.7 减速器单元
减速器组件包括谐波减速器,波发生器与电机输入轴固定连接,柔轮与扭矩传感器连接,刚轮与输出法兰固定连接。值得注意的是,柔轮与扭矩传感器之间有一个摩擦结构件,粗略判断是为了增加扭矩传感器的识别精度(用螺栓固定时每个连接件之间的螺栓孔位都存在孔隙,柔轮在正常工作中会发生弹性变形,再加上协作的特点是碰撞检测,外力作用下可能会产生滑移,增加摩擦结构可以减少这两类的影响)。
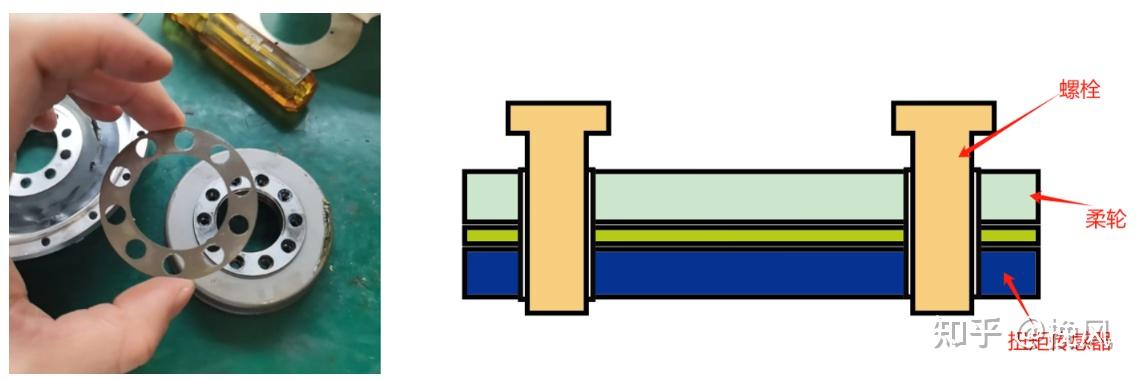
减速器的密封原理为:柔轮与波发生器输入轴之间通过旋转封(类似油封功能)进行密封,但我不理解为什么波发生器的外侧(靠近柔轮膜片)要有油盖,实际上油盖那侧拆机后油脂堆积很多,并没有起到防油作用。
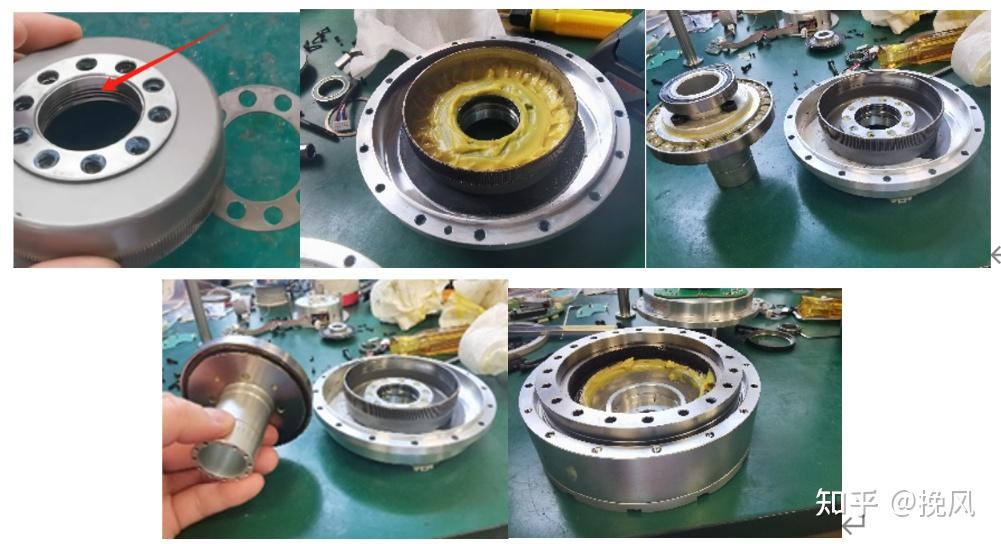
2.8 扭矩传感器
思灵关节的扭矩传感器放在内部的机械关节上,原因是为了保证关节和机械臂装配时,扭矩传感器不受外界冲击碰撞而损坏,而且扭矩传感器的电源和信号线从关节旁边而不是通过关节中心孔连接到关节右端电路板上,使得扭矩传感器线缆与关节线缆分开布置,互不干扰信号;而且线缆长度更短,利于信号传输;关节中心孔线缆数量少,孔径变小,关节结构更加紧凑。
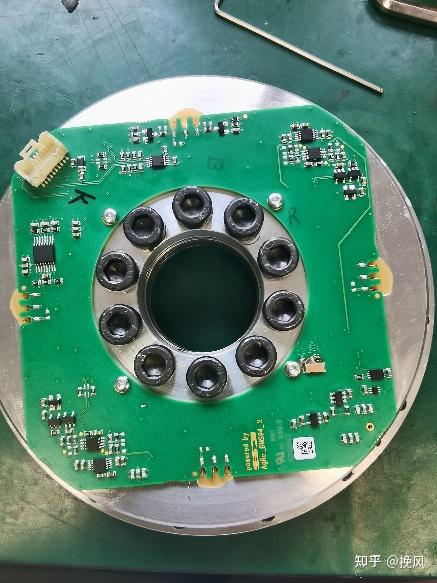
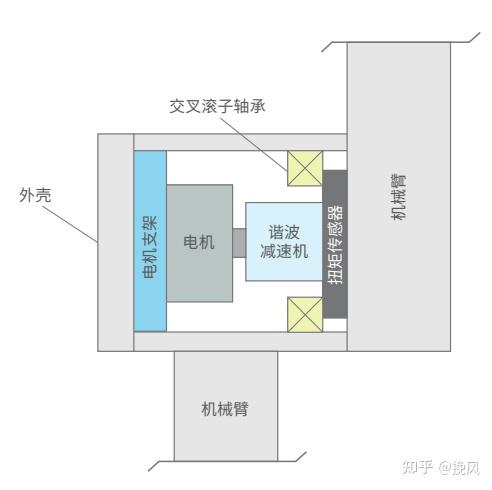
图13右侧为典型的扭矩传感器位置,可以直接感受外界负载的变化,但是思灵关节的扭矩传感器固定在内侧,压阻式应变片连接到挠曲件区域,采用惠更斯通电桥配置,将机械应变转换为Mv/V输出,但是该挠曲件区域封存在关节內部,内侧直连柔轮(固定件),外侧直连外壳(固定件),其挠曲变形是检测柔轮在传递过程中的反向扭矩力吗?那外力通过法兰传递到刚轮,再由刚轮通过齿啮合传递给柔轮,柔轮固定在扭矩传感器上,检测到的力是否与外力存在某些损失?齿部啮合时间越长,扭矩传感器的噪声越大,精度应该会直接下降吧。
2.9 轴承的跨距支撑
在该关节结构中,主要有三处轴承跨距支撑(关节还有1处是过线筒与磁环的轴承,该轴承未计入跨距支撑轴承内),如图14所示,谐波减速器的波发生器输入轴两端各用一个61806深沟球轴承做支撑,整个关节与末端法兰(法兰上连接负载或者机械臂)的接合处使用一个RA10008C交叉滚子轴承做支撑。其中输入轴两端做有两点支撑,但是输入轴与电机轴直接相连,电机轴系统轴向有波形弹簧存在弹性力,当弹性力无法与热膨胀力、轴向力等相互平衡时,将导致波发生器存在轴向窜位移动,从而对减速器啮合产生影响,因此波弹和垫片的选择将直接影响此处减速器的啮合质量。

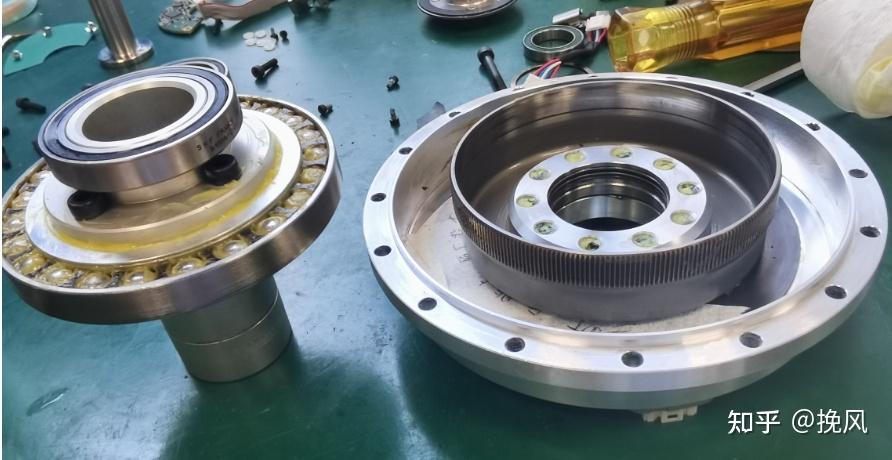
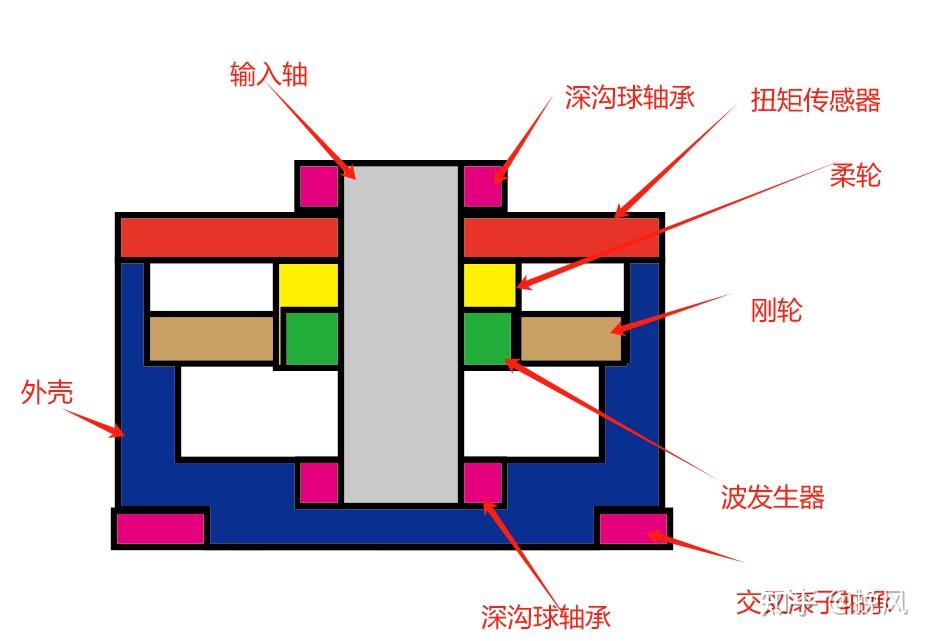
对于电机来说,电机的定子外壳与减速器外壳等固定连接在一起,在不计螺栓连接的刚性问题下,尾部的交叉滚子轴承和前端磁环的深沟球轴承可起到一定的双点支撑作用;但是电机的转子仅依靠波发生器的输入侧固定连接后,在轴伸处存在一处支撑,属于悬臂支撑结构,稳定性存疑。
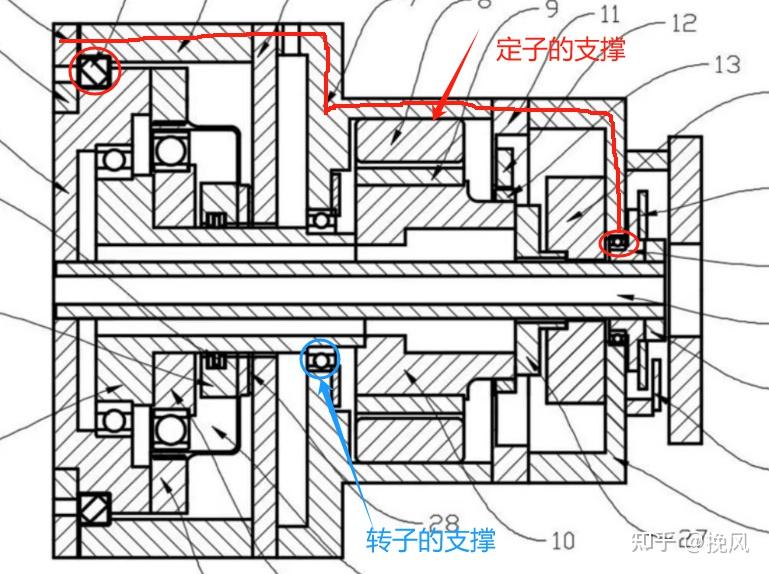
最后是交叉滚子轴承,交叉滚子轴承主要决定了关节可承受的倾覆力矩状态,在关节内侧,需要考虑电机外壳模块与所连连杆或负载的负载力矩;在关节外侧,需要考虑法兰所连连杆或负载的负载力矩,这两个倾覆力矩是对交叉滚子轴承是否有效支撑的重要校核项。
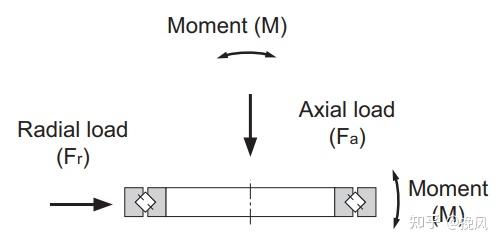
参考文献
[1] 北京思灵,一种机械臂关节[P] CN110919688A,20200327.
零差云控的拆机更关注于一些细节设计,起篇前首先要致谢一下 大头哥
@吴上伟 的倾情相授。
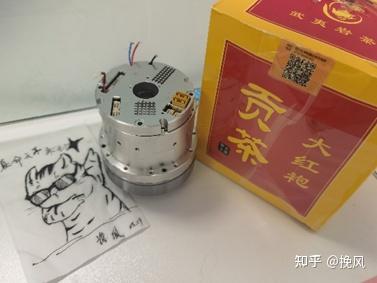
1 关节整体结构
所拆关节为eRob80H,关节参数如下:
关节型号 | eRob80H | |
---|---|---|
谐波减速机-速比 | 17-100 | |
启停峰值扭矩 | Nm | 70 |
额定扭矩 | Nm | 31 |
瞬间容许最大扭矩 | Nm | 143 |
输出端峰值转速 | rpm | 30 |
电机功率 | W | 146 |
转子惯量 | g·mm² | 70637 |
外径X长度 | mm | 80*84.2 |
重量 | kg | 1.25 |
供电电压 | V | 48±10% |
通孔直径 | mm | 18 |
IP等级 | IP54 | |
输出端编码器分辨率 | Bit | 20 |
输出端重复/绝对定位 | 角秒 | ±7/±15 |
关节的整体结构可参考专利“CN210650737U 一种机器人关节模组”和“CN218428419U 双轴承支撑的关节模组及关节机器人”。其关节结构从左到右(从下往上)依次是模组端盖、电路板、电机定子外壳、双磁编、电机转子轴、支撑轴承、制动器、谐波减速器、输出轴等结构,详见图1.
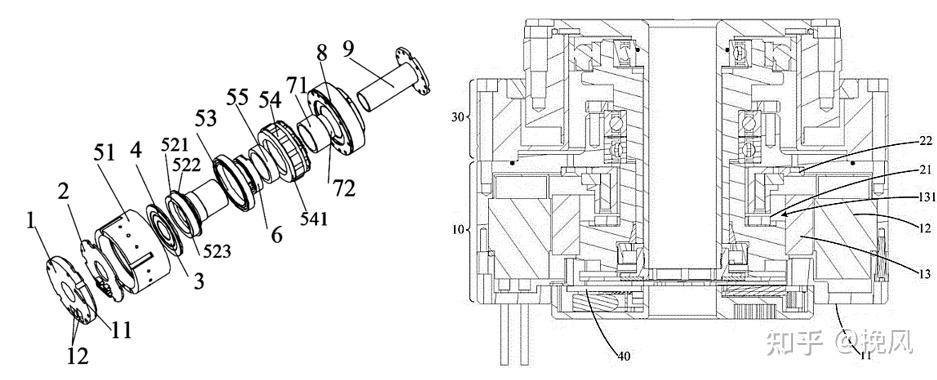
2 双编码同平面嵌套设计
2.1 双编码的作用和必要性
协作机械臂关节传动机构一般由电机侧编码器、输出侧编码器组成,按照金刚科技的技术文章来看,电机侧编码器可为增量式或单圈绝对式,主要用于电机速度PID、FOC闭环控制及电机位置检测,中等分辨率(满足无刷电机的伺服控制即可)、高精度(精度是最重要的,要与减速后输出侧的精度或应用相匹配),另外电磁式编码器工作时可能会与电机的转子磁铁相互干扰,可能会在电机侧使用多圈增量式光栅编码器;输出侧编码器可为单圈或多圈绝对式,用于输出端位置闭环控制,高分辨率,绝对定位精度要求并不特别高。
双编的算法是通过双编码器的实时位置偏差估计外力矩,当输出侧收到外部扭矩,输出侧编码器测量到微小变化,在减速比传递作用下,电机侧的编码器还未发生变化。通过对比可得到机械臂输出侧的微小用力,从而反馈给驱动器,若用户打开了拖动示教则开始调节电机跟随受力;若没有,则转动电机补偿外部受力以保持位置恒定。当动态控制时,控制器在得到电机编码器的数据后,可计算出输出轴的理论位置,然后与输出轴编码器的实际位置数据对比,得到外部受力大小,从而驱动器进行后续控制。
注意到ABB的双编运动控制文档中详细介绍了双编码器反馈技术,与协作双编原理接近:分别将一个编码器装在负载上,另一个编码器装在电机上,负载上的编码器用于测量位置,即闭合驱动控制系统中的位置回路,电机上的编码器仅用于测量电机的运行,即闭合驱动控制系统中的电流回路和速度回路,这种组合提供了高位置精度,排除了机械顺从性、间隙、滑动等相关的稳定性问题。
其中的示例如图2所示,图中伺服电机内置旋转编码器,该编码器用于与电机进行通讯,用于控制转矩、速度和位置。由于有电机编码器,可以获得精确的电机位置,通常来说,电机侧采用多种不同的反馈技术,包括增量编码器+霍尔传感器、解析器、BISS、SSi、SmartAbs、EnDat和Hiperface.由于传动环节的间隙、顺从性、磨损与热膨胀,负载位置只能从电机位置计算得到估计值。为了改善负载位置的精度,在系统的负载端增加绝对编码器。
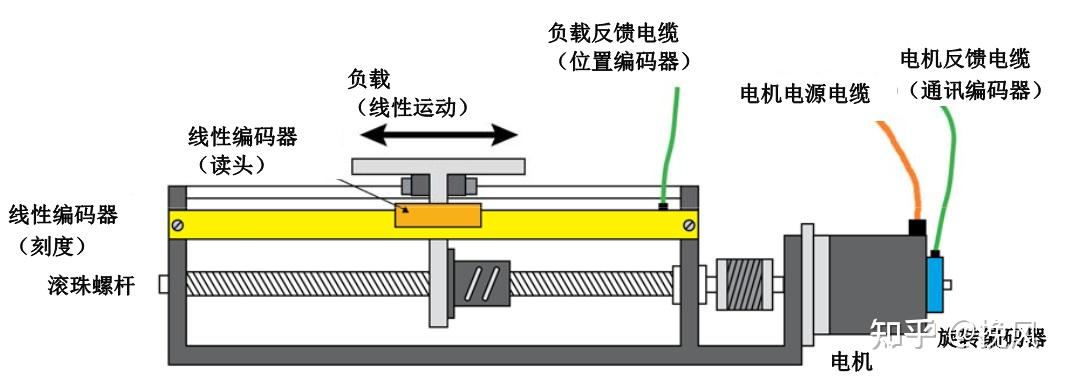
因此推测在运动控制中,双编最大的作用还是充当补偿作用,估计力矩的方式考虑到关节动态特性和刚度特性的复杂性,估算偏差较大,目前的技术水平不如力矩传感器更有效。
2.2 双编码器带来的安装问题
采用双编,编码器就必须分别安装在输入、输出侧,则需要考虑结构复杂度与走线复杂度。目前综合机电结构的考虑,通常采用的结构拓扑图如图3所示,通过中空轴将输入输出编码器置于同侧,解决了固定与走线的问题。
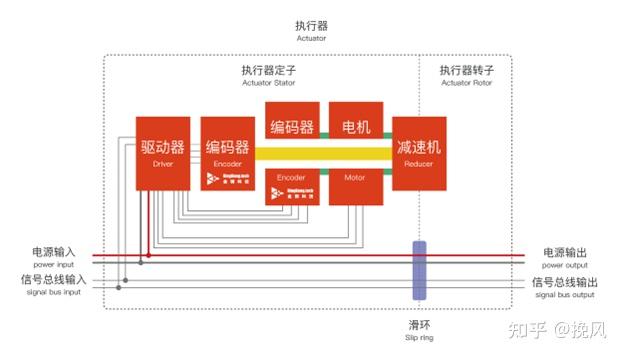
考虑到轴向空间的空间利用,零差云控采用同一平面同轴嵌套的安装方式,详见“CN108638096A 双码盘编码器及应用该双码盘编码器的伺服关节”,特点在于高速端和低速端编码器位于同一平面、同轴嵌套设置,比上下设置两个编码器来说关节体积更小。
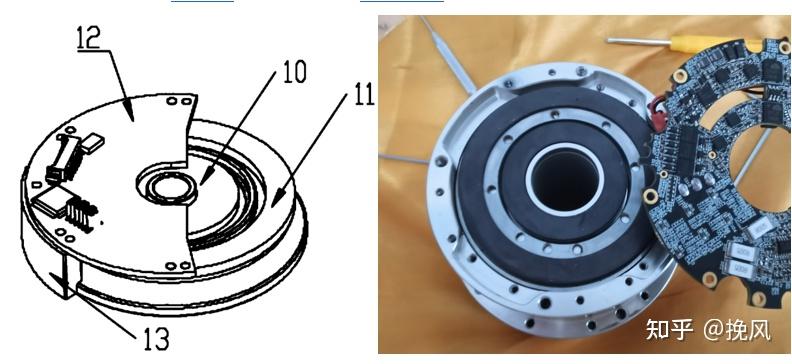
按照官方提到的安装要求,码盘同心度误差对编码器精度影响最大。值得推敲的是,编码器芯片PCB板通过螺纹锁固在外壳上,仅依靠螺栓定位固定,将会造成较大的偏距。其次,减速器输出轴亦通过螺栓端面固定,没有其他辅助定位件。于是,这同轴度的0.05mm是如何保证的就不得而知了,通过测量+装配吗?
分体式编码器码盘如何安装?-常见问题-零差云控www.zeroerr.cn/issue/47.html?t=1715392431168
通常来说,可以通过在PCB上设定销孔,然后用销做读头的定位;而对于高低速磁环,则可以通过轴承做一个辅助定位,相对来说通过机加面保证安装精度会更好一些。
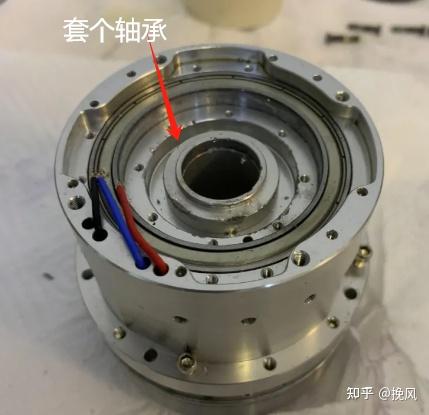
2.3 散热设计
由于协作关节追求结构紧凑性,但往往热密度会变大。注意到在零差云控的控制PCB板的封装端盖上,分别在主控芯片和模拟电路位置开了两处散热孔结构;在另一家关节的设计中,注意到电机定子绕组的外壳上也用了类似的散热肋板翅片的型式,增加散热面积来达到热设计目的。
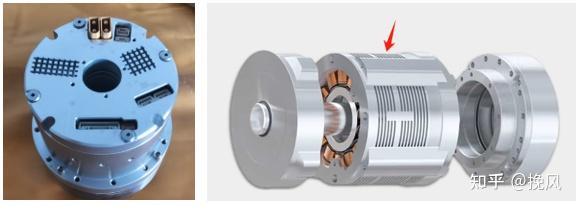
2.4 “意想不到”的设计
(1)输出轴装配磁环的位置,用的竟然是一个螺纹连接(应该是细牙螺纹)
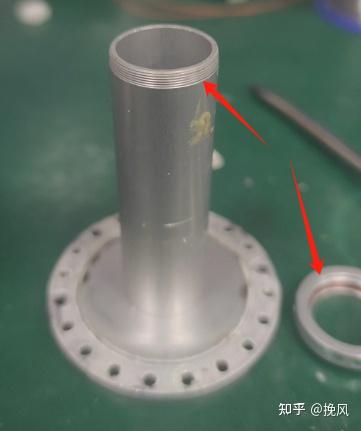
(2)谐波减速器的波发生器与电机轴的连接
由图8可以注意到,需要先将波发生器从左侧装入柔轮,然后再将电机轴从右侧装入波发生器的内孔中。
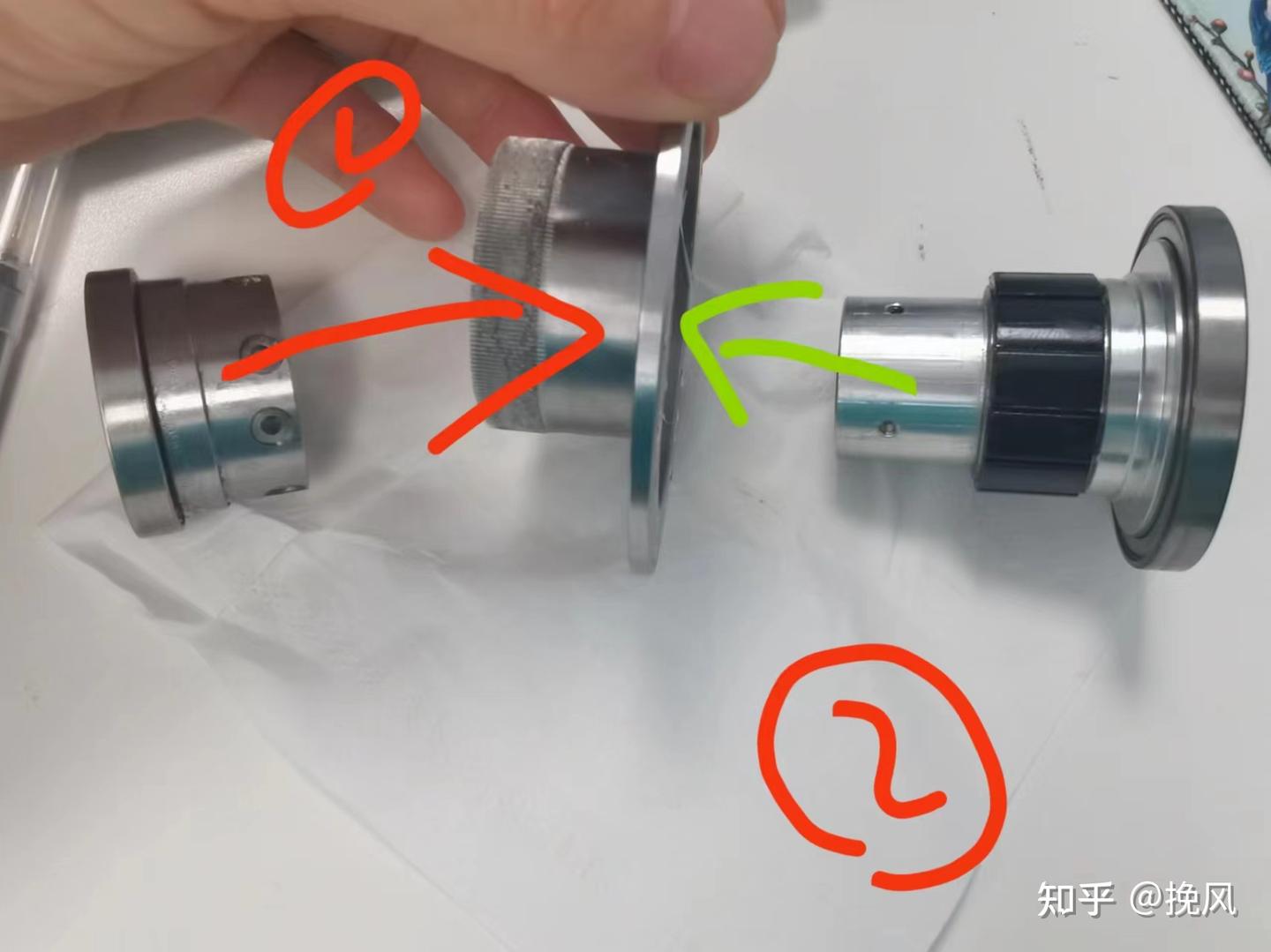
波发生器与电机轴的固定是由轴上的沉头通孔+螺纹通孔固定的,但是安装的时候由于柔轮的长径比深一些,安装后安装孔会被柔轮挡住而无法装配,此时需要将波发生器往柔轮内部推深一些,直至露出安装孔位,如图9所示。和谐波厂家沟通后,认为该方式会损伤减速器,是非标准安装方式,应避免采用。
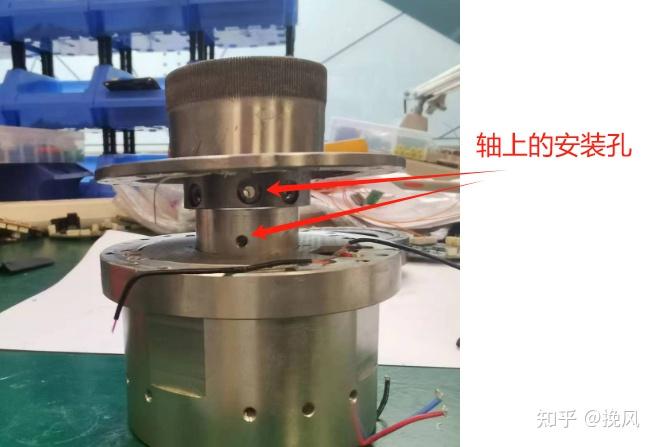
还有另一种方式是将波发生器的柔性轴承拆下来,把轴套固定后再装波发生器的轴承,但是厂家认为该方式一方面来料两者是装在一起的,拆卸重装可能会损坏波发生器轴承;另一方面,安装柔性轴承是需要使用工装的,在安装到电机定子上的电机轴来说,工装的可使用性不大,除非特制工装。
考虑到该结构应该是早期设计,存在不合理的可能性,因此认为是波发生器内推露出孔位,安装后再将波发生器推出至适当位置来实现装配,如图10所示。
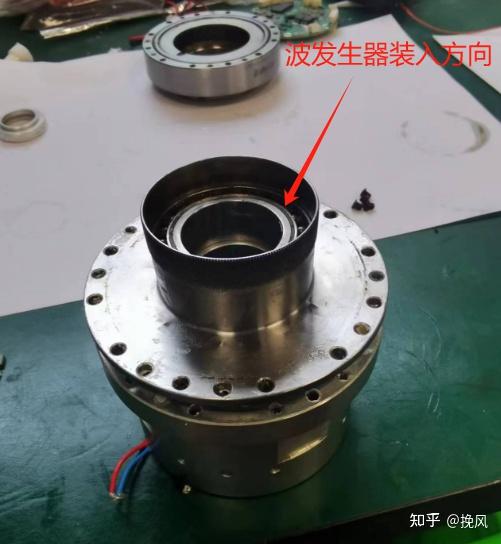
(3)单轴承支撑
电机输入轴的整体支撑仅靠左侧的6809Z深沟球轴承在支撑
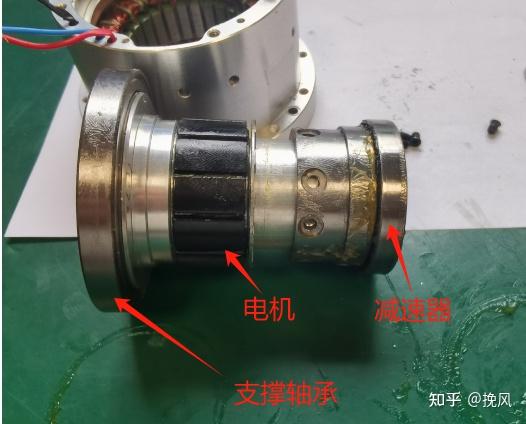
大致画了一个示意图,这种支撑作用下,波发生器的扰动会比较大,柔轮刚轮啮合处会受到多余的外力,从而影响传动精度和减速器寿命,应该是属于不合理的结构。
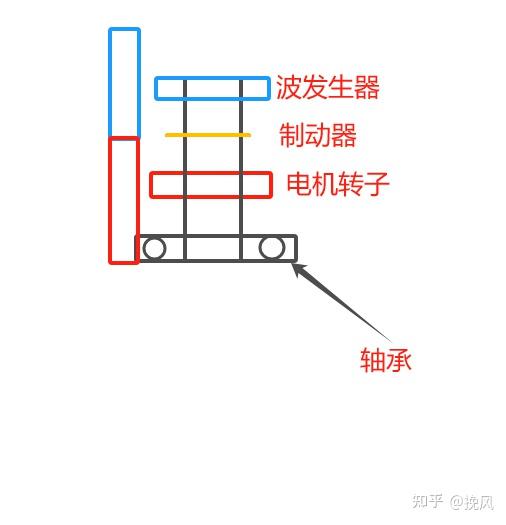
输出轴无任何轴承辅助支撑,加上长度的影响,输出侧码盘的动态精度应该会比较差。
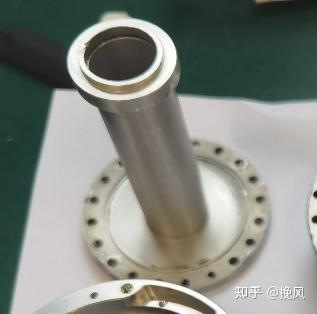
(4)抱闸
零差云控采用摩擦片式抱闸(eBreaker),是目前见到的比较紧凑的抱闸结构。查阅专利“CN218659159U,摩擦式制动器的关节模组及关节机器人”,其抱闸原理与电磁摩擦片式同理。
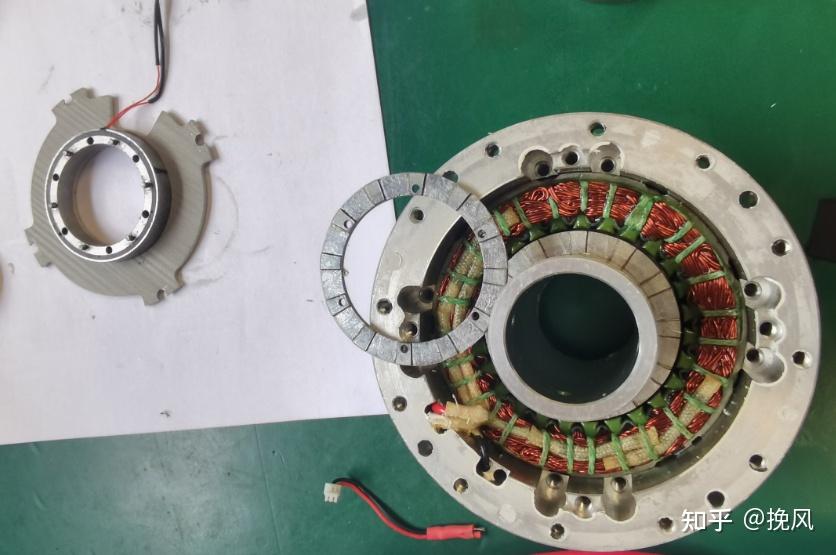
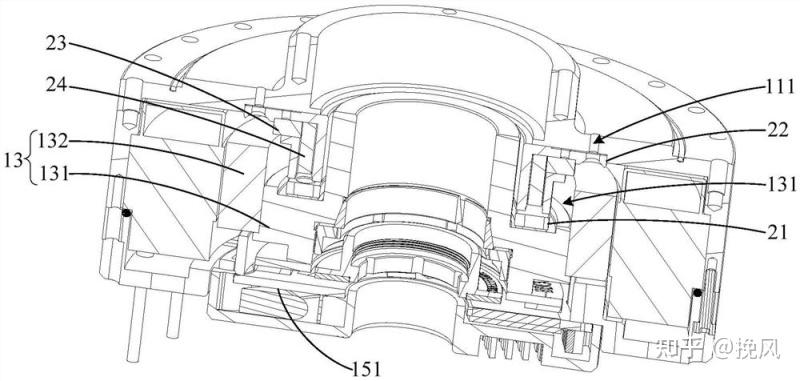
2.5 密封设计
关节主要防止减速器内部的润滑脂流出,其密封主要有
(1)柔轮法兰面与电机定子外壳连接面的密封:采用密封胶(白色的,像1211密封胶)
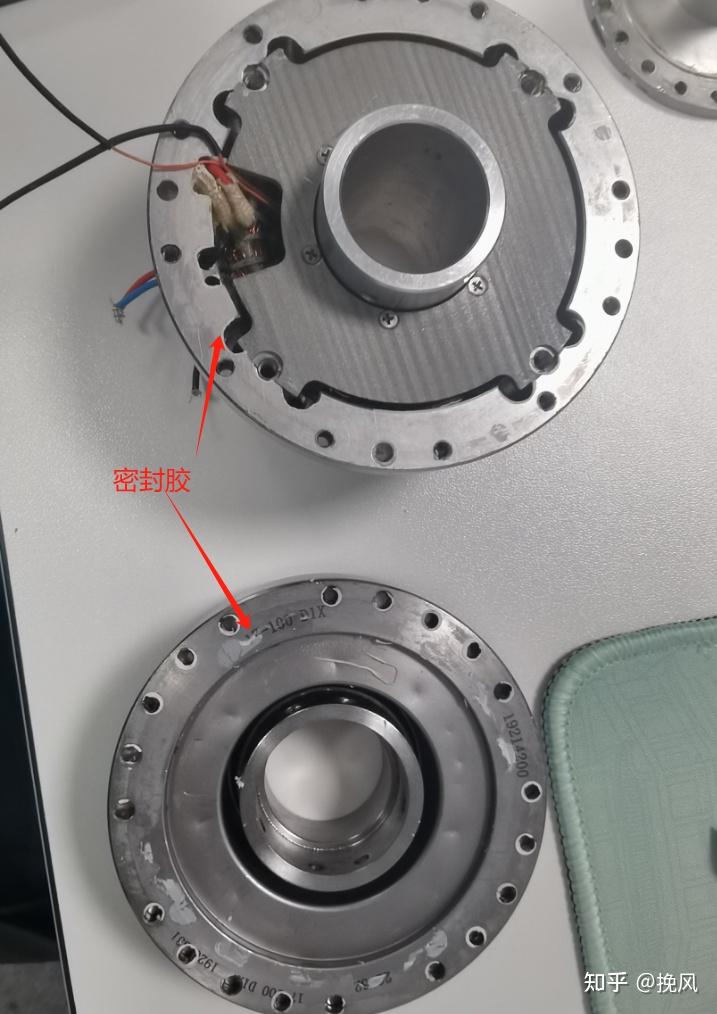
(2)柔轮法兰面与减速器外壳的连接:O型圈密封
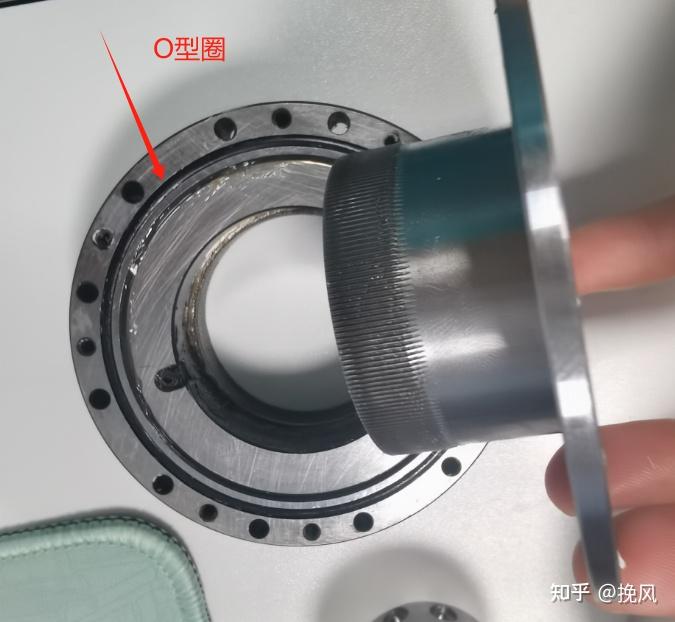
(3)减速器输出轴与波发生器连接面:密封胶(螺纹孔也用密封胶封了)+密封槽(类似迷宫槽、O型圈沟槽一样)
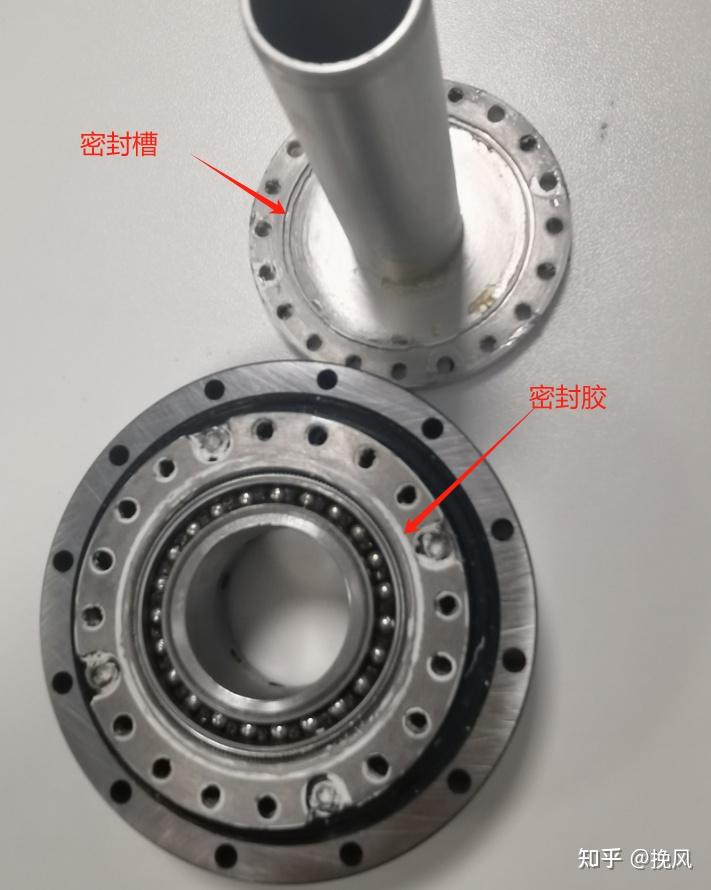
(4)交叉滚子轴承内部与固定件:油封密封
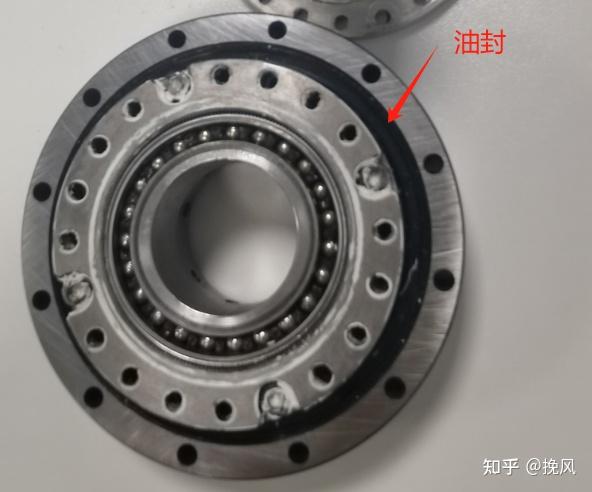
参考文献
[1] CN210650737U 一种机器人关节模组
[2] CN218428419U 双轴承支撑的关节模组及关节机器人
[3] CN108638096A 双码盘编码器及应用该双码盘编码器的伺服关节
[4] ABB运动控制技术手册“Dual encoder feedback control on motion drives Rev A”
[5] CN218659159U,摩擦式制动器的关节模组及关节机器人
评论0